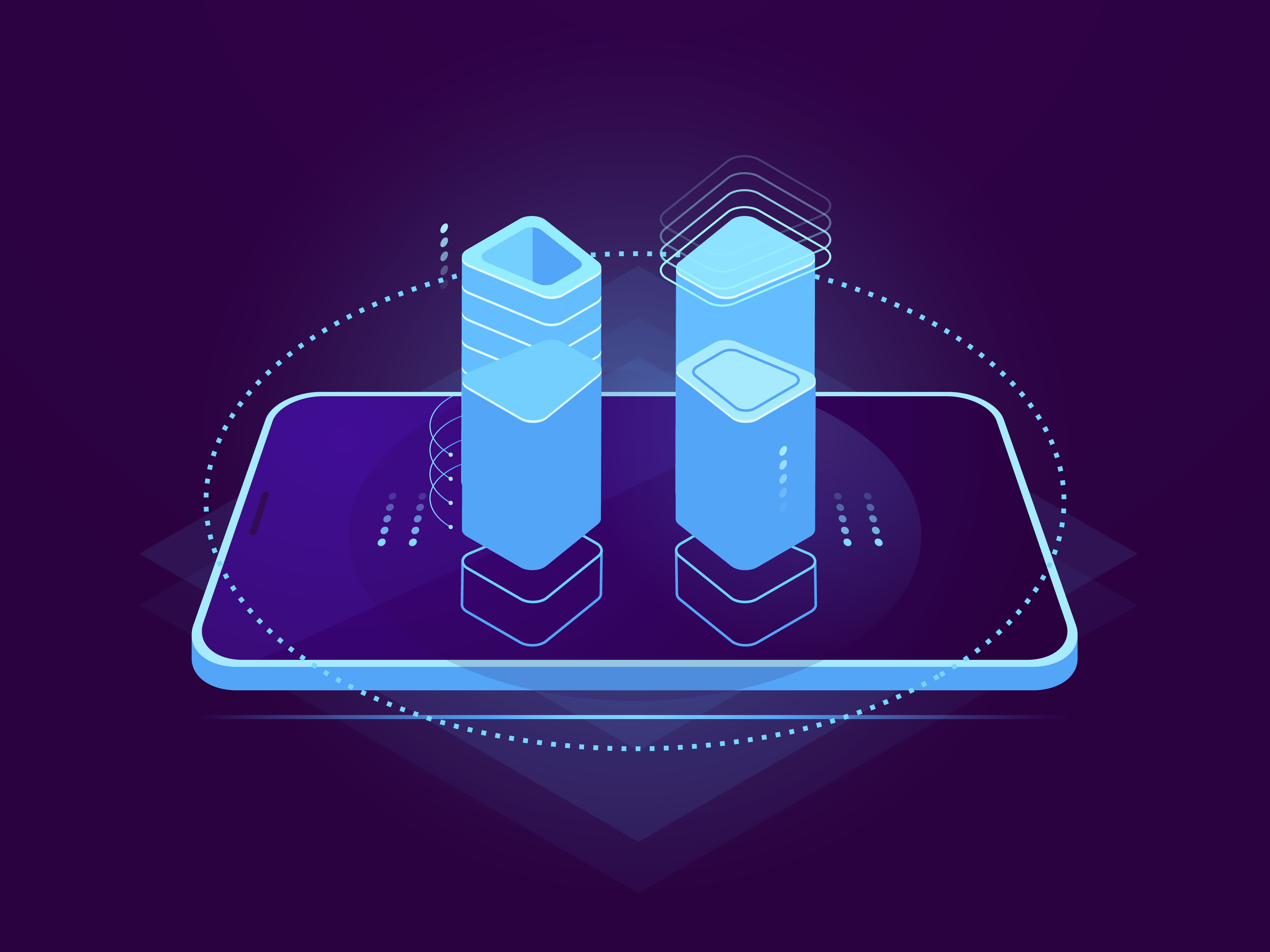
1. Welcome to the Future of Manufacturing
Imagine a world where machines never break down unexpectedly, where factory downtime is a thing of the past, and where your coffee maker tells you it needs descaling before it stops working. Sounds like science fiction, right? Well, buckle up, because the future is here, and it's all thanks to something called "digital twins."
In the world of manufacturing, a game-changing technology is revolutionizing how we build, maintain, and optimize our machines. It's called digital twin technology, and it's like giving our physical machines a virtual doppelganger. But don't worry, these twins aren't here to replace us – they're here to make our lives easier and our factories smarter.
2. What Are Digital Twins? Demystifying the Virtual Doppelgangers
So, what exactly is a digital twin? Think of it as a virtual mirror of a physical object. It's a highly detailed digital replica of a real-world machine, process, or even an entire factory. This virtual twin lives in the cloud, constantly updated with real-time data from its physical counterpart.
Jargon Buster: A digital twin is defined as "an integrated multiphysics, multiscale, probabilistic simulation of an asset that can reflect the life of its corresponding twin using physical models and data". In simpler terms, it's a super-smart, always-learning digital copy of a real thing.
3. The AI Magic Behind Digital Twins
Now, you might be wondering, "How does this digital twin know what's going on with the real machine?" That's where the magic of Artificial Intelligence (AI) and the Internet of Things (IoT) comes in.
Imagine your digital twin as a very attentive student, constantly taking notes. Sensors on the physical machine (that's the IoT part) feed data to the digital twin. The AI then analyzes this data, learning the machine's normal behavior and spotting any deviations.
Did You Know? The concept of digital twins originated in the early 2000s but has gained significant traction in manufacturing since 2018.
Practical Example: Let's say we have a manufacturing robot. Its digital twin would receive data about the robot's movements, the force it applies, the temperature of its motors, and more. If the robot starts using more force than usual for a particular task, the digital twin would flag this as a potential issue before it becomes a problem.
4. Predictive Maintenance: From Fortune-Telling to Data-Driven Decisions
One of the most exciting applications of digital twins is in predictive maintenance. Traditional maintenance is like taking your car to the mechanic every 5,000 miles, whether it needs it or not. Predictive maintenance, on the other hand, is like having a mechanic riding along with you, telling you exactly when something needs attention.
Digital twins take this to the next level. They don't just predict when maintenance is needed; they can simulate different scenarios to find the best maintenance strategy. It's like having a crystal ball that not only sees the future but helps you choose the best one!
Success Story: A study published in Heliyon journal showcases how digital twin technology has been successfully applied in various industries, including intelligent manufacturing, power industry, construction, aerospace, and shipbuilding.
5. The Ripple Effect: How Digital Twins Are Transforming Manufacturing
The impact of digital twins on manufacturing is nothing short of revolutionary. Here's how:
- Improved Efficiency and Reduced Downtime: By predicting issues before they occur, digital twins help keep production lines running smoothly.
- Cost Savings and Extended Equipment Lifespan: Timely maintenance means less wear and tear on machines, saving money in the long run.
- Enhanced Safety and Quality Control: Digital twins can simulate dangerous scenarios without putting workers at risk and ensure consistent product quality.
- Environmental Benefits: By optimizing processes, digital twins help reduce waste and energy consumption.
6. Implementing Digital Twins: A Step-by-Step Guide for Businesses
Ready to bring your machines into the digital age? Here's a simplified roadmap:
- Assess Your Needs: Identify which processes or machines would benefit most from a digital twin.
- Choose the Right Technology: Select sensors, software, and platforms that fit your needs and budget.
- Train Your Team: Foster a data-driven culture and ensure your staff understands the new technology.
- Start Small, Think Big: Begin with a pilot project and scale up as you see results.
- Overcome Challenges: Be prepared for hurdles like data integration issues or resistance to change.
7. The Future is Now: Real-World Applications and Success Stories
Digital twins are already making waves across industries:
- In the automotive industry, manufacturers use digital twins to simulate and optimize production lines.
- Aerospace companies create digital twins of entire aircraft to improve design and maintenance.
- Energy companies use digital twins to optimize wind farm layouts and predict turbine maintenance needs.
As one expert puts it, "Digital Twin for PdM (Predictive Maintenance) enables accurate equipment status recognition and proactive fault diagnosis".
8. Conclusion: Embracing the Digital Twin Revolution
Digital twins are more than just a cool tech trend – they're a powerful tool that's reshaping the manufacturing landscape. By bridging the physical and digital worlds, they're helping businesses reduce costs, improve efficiency, and stay ahead of the competition.
Ready to twin your way to success? The future of manufacturing is here, and it's digital. Whether you're a small workshop or a large factory, there's a digital twin solution out there for you. So why wait? Start your digital transformation journey today and give your machines the virtual sidekick they deserve!
Curious about how digital twins could revolutionize your business? Reach out to Anablock today and take the first step towards a smarter, more efficient future!